Last updated on April 3rd, 2024 at 04:41 pm
An electrolytic capacitor uses an electrolyte to achieve a larger capacitance than other capacitor types. Unlike the regular ones, which use two conductors separated by a dielectric material, an electrolytic capacitor uses an electrolyte as one of its plates.
However, they are also subject to failure due to a variety of issues. In this article, we will discuss how they fail. We’ll also share some tips to prevent this.
Table of Contents
How does an electrolytic capacitor fail?
The vast majority of failures are caused by one or more of the following mechanisms: dry-out of the electrolyte, loss of adhesion between the electrode and electrolyte, corrosion of the electrode, or breakdown of the dielectric.
- Dry-out occurs when the electrolyte evaporates, leaving only a solid layer of oxide on the electrodes. This can be caused by excessive heat, overcharging, or extended storage in a low-humidity environment.
- Loss of adhesion can be caused by physical shock, vibration, or prolonged exposure to high temperatures.
- Corrosion is typically caused by exposure to chemicals or high humidity.
- And finally, the breakdown of the dielectric is typically caused by electrical stress (e.g., overvoltage or reverse voltage).
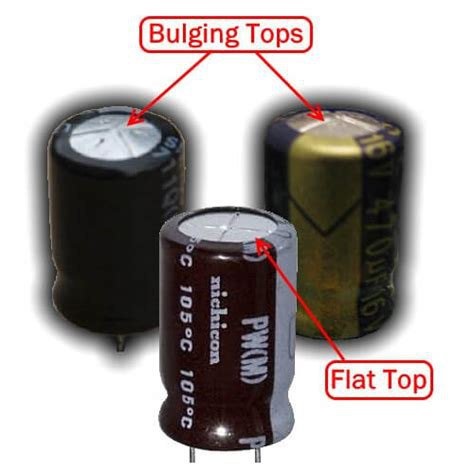
Detecting the failure symptoms
The failure of the electrolytic capacitor in a circuit can cause a short circuit(due to mechanical failure), open circuit(manufacturing defect, mechanical failure), loss in capacitance, and high ESR.
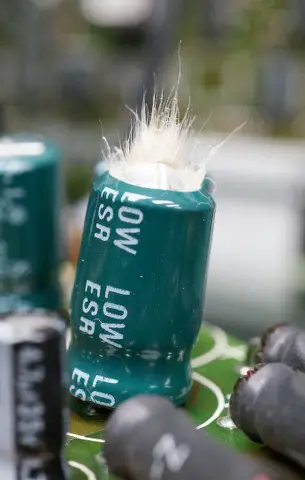
Short Circuit: Short circuits between the electrodes can occur due to vibration, shock, or stress on leads. In addition, applying voltages over the recommended voltage, excessive ripple, or pulse current can all contribute to this problem.
Open Circuit :
- When the capacitor is mounted in a circuit with excessive force or gets subjected to vibration or shock while in use. In these situations, the lead wire and tab connection may get bent or twisted, which eventually results in an open circuit.
- If the sealing component is not maintained properly, the electrolyte can evaporate and result in an open circuit.
- Operating at temperatures over the recommended range, exposure to excessive heat conveyed through P.C. board patterns, or extended use can all lead to sealing material breakdown.
- Due to an increase in temperature inside the capacitor caused by an improperly applied ripple, the electrolyte vaporizes and leaks through the end seal material. The electrolyte will thereafter get dry, leading to an open circuit.
Capacitance Drop, High Loss (High ESR)
- Continuous reverse voltage is used
- If it is subjected to extreme charge and discharge
- Generation of gas produced by reverse voltage, over-voltage, extreme ripple, or AC voltage
- Current above the maximum rated ripple is continually applied.
Increasing the capacitor’s lifespan
Electrolytic capacitors made of aluminum deteriorate over time. A vent is a common feature of electrolytes that lets extra gas escape. The electrolyte may dry out as a result of this escape, lowering the its performance.
Precautions should be taken to increase their lifespan. To extend the life of an aluminum electrolytic capacitor, follow these four golden rules:
Operate the capacitor within its voltage range:
- Keep the applied voltage within the specified limit.
- Electrolytic capacitors should only be operated at roughly 50% of their maximum ratings (as per design guidelines)
- If the maximum limitations are surpassed, the leakage current will increase and the component may fail.
Stay within its current rating:
- An electrolytic capacitor will often be required to supply large levels of ripple current in applications like smoothing capacitors in a power supply.
- Make sure that it can handle the current demand.
- Ensure that it is operating within its current limitations and is not getting too warm while in use.
Never reverse bias the capacitor
The leakage current would be substantially higher in this case which may result in catastrophic failure and breakdown.
Operate at low temperature:
- Aluminum electrolytic capacitors are all affected by heat.
- As a general rule, the component’s life expectancy is reduced by 50% for every 10°C above 85°C.
Although aluminum electrolytic capacitors have a limited lifespan, if these guidelines are followed and they are operated well within their ratings, the lifespan can be increased toward its maximum.
How to reform an unused aluminum electrolytic capacitor?
If electrolytic capacitors are left without use for more than 6 to 18 months, the aluminum oxide dielectric insulation can degrade. In this case, the capacitor needs to be reformed.
It is not advisable to apply the full voltage under these conditions since the leakage current will be high and may cause the capacitor to generate a lot of heat, which in some cases may cause it to fail.
The normal method to reform the capacitor includes:
- Applying a small, regulated DC charge at a controlled current over an extended period. This process allows the electric field to interact with the electrolyte by gradually raising the voltage level.
- The aluminum oxide layer on the anode plate will be replenished as a result of this interaction. The capacitor can be used right away once it is finished.
- Apply the capacitor’s working voltage through a 1.5 k ohm resistor, or perhaps less for lower voltage capacitors. This should be applied for an hour or more until the leakage current has decreased to an acceptable level and the capacitor’s voltage reaches the applied value.
- After that, this voltage should be applied for an additional hour to prevent damage from the remaining charge, it can then be gradually discharged by an appropriate resistor.