Last updated on March 23rd, 2024 at 01:40 pm
There are four methods to start a squirrel cage induction motor. These are Direct On-Line (DOL), Stator resistance, Auto-transformer, and Star-delta starting, while for a slip-ring induction motor, we prefer rotor resistance starting.
Now, you might think that an induction motor is self-starting, then why do we need induction motor starting methods? Right? Don’t worry because this article will clear all your doubts on the induction motor and its starting methods. So, keep on reading till the end.
Table of Contents
Why do we need induction motor starting methods?
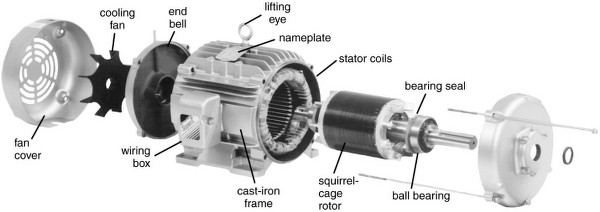
On giving a three-phase AC supply to an induction motor, a rotating magnetic field gets produced. This field links with the rotor conductors and creates torque for the rotor. In this way, an induction motor starts. But, this process requires a high inrush current from the AC mains. So, what’s the problem with this?
The high current requirement for a particular load may create severe voltage drops in the AC distribution system. It also affects other electrical loads connected within the same system. It can even burn the motor windings. In extreme cases, it may lead to a complete blackout.
But, we can easily avoid this problem if we can limit the starting current of the induction motor. Thus by employing induction motor starting methods, we can reduce the starting current to a safe value.
What are these induction motor starting methods?
All the induction motor starting methods use a starter to limit the starting current to a safe value. So for a squirrel cage induction motor, these starters can be either one of the following:
- Direct On-Line starter (DOL)
- Primary or stator resistance starter
- Auto-transformer starter
- Star-Delta starter
For slip ring induction motors, we use a more efficient starter:
- Rotor resistance starter
Let us discuss each one of these methods in a bit more detail.
Direct On-Line Starter
It is the most economical method to start low-rated induction motors (i.e., up to 1.5kW). This starter applies full voltage to the induction motor. Hence the rated full load current flows through the motor windings.

Now, isn’t it contradictory? Above we stated that it is essential to limit the starting current, and this starter doesn’t suppress the starting current at all? So, the point to understand here is that this method is limited to low-rated motors.
The starting current demand for these motors is within the permissible limits and doesn’t create a high voltage dip in the supply system. Hence, there is no issue in applying a full-rated voltage to the motor terminals.
Protection
This starter consists of an overvoltage, under-voltage, and thermal protection circuit. So, if there are any fluctuations, the control circuit disconnects the motor from the AC supply mains. Thus, protecting the induction motor.
Advantages
- It is the most economical starter.
- It provides a high starting torque.
- They do not require any special arrangements for starting the motor.
Disadvantages
- It is suitable only for low-rated induction motors.
- High current stress appears across the motor windings.
Primary resistance starting
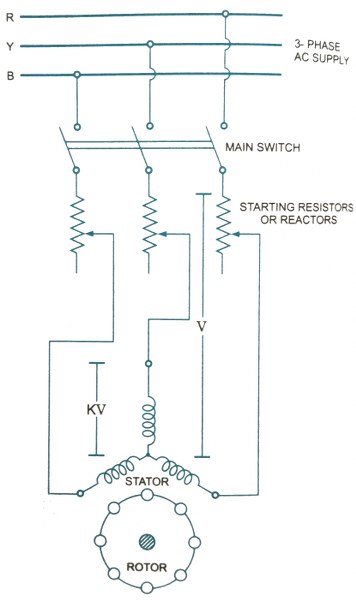
This method uses resistors to create a voltage drop and hence reduce the starting current to the motor. Each stator lead consists of a variable resistor in series with it.
So, during the starting, the complete resistance is present in the circuit. It causes a voltage drop, and thus, a reduced voltage appears across the motor terminals. The resistor gradually cuts out as the motor picks up speed.
When the motor attains full speed, all the resistances get disconnected, and a rated voltage appears across the motor terminals. So, with this starter, the starting current and starting torque gets reduced by a square ratio.
Advantages
- It provides smooth acceleration of the motor.
- This method gives a higher power factor at starting.
- For low-output loads, this method is less expensive than the auto-transformer starter.
Disadvantages
- The resistors dissipate heat.
- For varying loads, adjusting voltage in this method is not easy.
Auto-transformer starter
In all the induction motor starting methods, the aim is to reduce the starting voltage and hence, the starting current. In this method, an Auto-transformer does this job. The auto-transformer consists of tapping at 50, 60, and 80% points. So, initially, a small fraction of full rated voltage appears across the motor terminals.
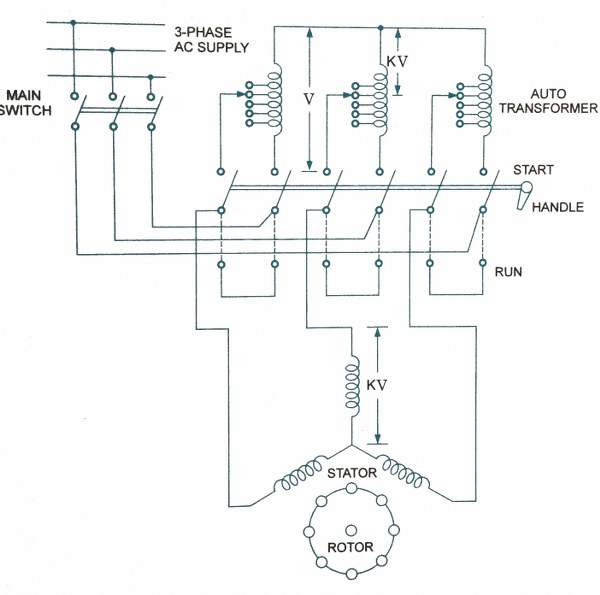
Selecting a reduced voltage reduces the starting current for the motor. As the induction motor picks up speed, a mechanism shifts the tapping to increase the applied voltage.
When the induction motor attains full speed, it finally disconnects the auto-transformer from the circuit, and thus, the rated voltage appears across the motor terminals.
So, with this method, the line current and starting torque get reduced by a square ratio.
Advantages
- This method of speed control is applicable for both star and delta-connected motors.
- The internal losses of the starter are small.
- It gives a higher torque at the starting.
- It is suitable for long starting periods.
Disadvantages
- The starting power factor is low.
- Its cost is higher.
Star-Delta starter
This method reduces the voltage by physically reconfiguring the starter windings. So, during the starting, the windings are connected in star, and as the induction motor achieves full speed, a mechanism switches the circuit to delta-connected windings.

The star-connected windings reduce the voltage to 57.7% of line-to-line voltage. Hence, with the reduced voltage, the starting current decreases, and the motor starts safely.
As the motor attains full speed, a change-over switch disconnects the star-connected windings from the main supply and reconnects the delta-connected windings. The delta-connected windings do not reduce any voltage and allow full line-to-line voltage to the motor terminals.
This method reduces the starting current and starting torque by a factor of 1/3.
Advantages
- This method is cheap, effective, and efficient.
- It is suitable for high inertia loads.
- It requires no tap changers, and hence heat losses are low.
Disadvantages
- This method is only suitable for delta-connected motors.
- The reduction of voltage is fixed and has no flexibility.
Rotor resistance starter

The above-discussed induction motor starting methods are suitable for squirrel cage induction motors. So, does it mean that we can’t use them for a slip ring induction motor?
Well, all these induction motor starting methods can start a slip ring induction motor. But, instead of them, rotor resistance starting offers more benefits. This method requires a variable external resistance in each phase of the rotor circuit.
Working
The motor starts with a rated voltage across its terminals. The high resistance in the rotor decreases the starting current but increases the starting torque. As the induction motor picks up speed, the resistances gradually disconnect from the circuit. On achieving full speed, all the external resistance gets disconnected from the motor circuit.
Advantages
- It provides a higher starting torque.
- It gives a smooth and wide range of speed control.
Disadvantages
- It is only suitable for a slip ring induction motor.
- It requires more maintenance due to the presence of slip rings and brushes.